Top 5 Robotic Applications in the Aerospace Industry
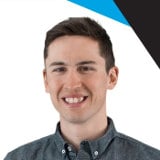
Posted on Feb 27, 2014 in Robotics
4 min read time
The aerospace industry is known to be very conservative. Companies typically use successful assembly methods that have already been proven to work in the past. In the past couple of years, however, the general attitude, in terms of assembly tasks, has really changed. In fact, since 2004, a complete mentality switch has been observed in the aerospace industry. Aircraft assembly companies like Boeing and Lockheed Martin tend to use robotics for some of their applications. Most of the tasks that require precision and rigidity on big parts are now executed by industrial robots. Since aircraft programs last from 10 to 30 years, the payback on a simple assembly task can be very beneficial. Industrial automation is now essential for the aerospace industry. Here are a few of the robotic applications in aerospace manufacturing.
1. Drilling and fastening
This is definitely the largest area for the use of robotics in the aerospace industry. In fact, manual drilling needs to be performed in three different steps (pilot hole drilling, final size drilling and reaming). Furthermore, the manual driller needs to use a big and complex jig, as well as powerful tools to perform these drilling steps in exotic materials such as titanium. By using robots, there is no need to design a specific jig—the robot uses a vision system to drill the hole(s) at the desired spot(s). Additionally, the drilling steps can be performed in a single pass. Robots are a huge time-saver for people when they can do a job in one pass.
“A fuselage needs thousands of holes drilled and drilling them manually is not feasible.” - Chris Blanchette, National Account Manager, FANUC Robotics.
2. Inspection
The inspection process in the manufacturing of any aircraft is critical. The tolerances are really tight and company requests for inspections are high. Several inspection procedures can be performed by robots. However, when holes are entirely drilled by robots, the process has to be approved. In some cases, the end-effector is equipped with a laser scanner and measuring probes. After the drilling operations, metrology equipment is used and the hole is then observed by the laser scanner which can gather different information. First, it is possible to measure the countersink quality and the surface characteristics in detail. Second, a non-contact bore probe can measure the hole diameter and the bore depth. The inspection process requires the detection of liquid shim blowout or exit burr, which can be detected by the scanner.
“To assemble a car using a carbon fiber composite material for an automotive body panel, for example, the panels are put together, but normally there isn’t a need to inspect them. No one will die in a crash from a crack in a body panel. It’s a quality defect, not a safety defect.” -Chris Blanchette, National Account Manager, FANUC Robotics.
With the implantation of composite material, non-destructive testing can be executed on several parts. Delamination, cracks and fastener inspections need to be done during the assembly process. With advanced ultrasonic and metrology inspection methods, some robots are designed to perform such applications. OC Robotics has developed an interesting flexible arm that can go into restricted spaces in the aircraft. With this kind of flexible arm, inspections are now more accurate and efficient.
3. Welding
Even if composite parts are increasingly popular in aircraft, metal parts still have their place in some applications. In fact, metal parts welding in assembly, such as turbine, need to be performed with precision. When using exotic metals, such as Titanium and Nickel-Alloy in motors, industrial robots are a must in order to do effective and accurate welds. Repeatability, rigidity and tight tolerance achievement are the main arguments when talking about robotic welding in aerospace applications.
4. Sealing and dispensing
Applying sealant, paint, metal and ceramic coatings on large fuselage or framing parts is difficult for a manual operator, because of the size of the parts. This is one of the reasons why robots are used for this kind of application. By putting robotic arms on rails, working cells can cover distances from 30 to 40 ft and several stories high. Aerospace companies tend to use more robotic methods including, from small to huge dispensing applications.
5. Rigid manufacturing
Rigidity is not an application itself, but can be considered as an advantage when using robots in aerospace manufacturing. In fact, over the years, robots are tending to be more precise than they have ever been. However, with tight tolerances, repeatability requirements and precise manufacturing processes, the robot has to be a more accurate. This is why most of the aircraft manufacturers use secondary encoders. In other words, they don’t trust the original encoders in the robot joint. When the robot is implanted, integrators install secondary encoders to know precisely the position of the robot joint.
“That allows better control of the robot by minimizing backlash to achieve a higher level of accuracy. Secondary encoders reduce settling time, because the robot can react more quickly in drilling applications.” -David Masinick, Aerospace Account Manager, KUKA Robotics Corp
The aerospace industry used to be known as a super rigid and conservative world. However, by seeing the enhancement opportunities that they could make on such a large assembly task, the choice was easy to make: switch to robotization. Aircraft constructors, such as Lockheed Martin, are claiming to enhance their monthly production. For example, they are now moving from three F-35 aircrafts produced per month to almost twelve. In a market where deadlines are tight, robot integration is a must. The most cost-effective way the aerospace industry can increase their production at a such a rapid rate is through robotics.
Leave a comment